Some big foreign car manufacturers are also setting up circular economy businesses, not just for batteries, but also for auto parts and cars. The effort is to recycle materials from used cars for fresh production
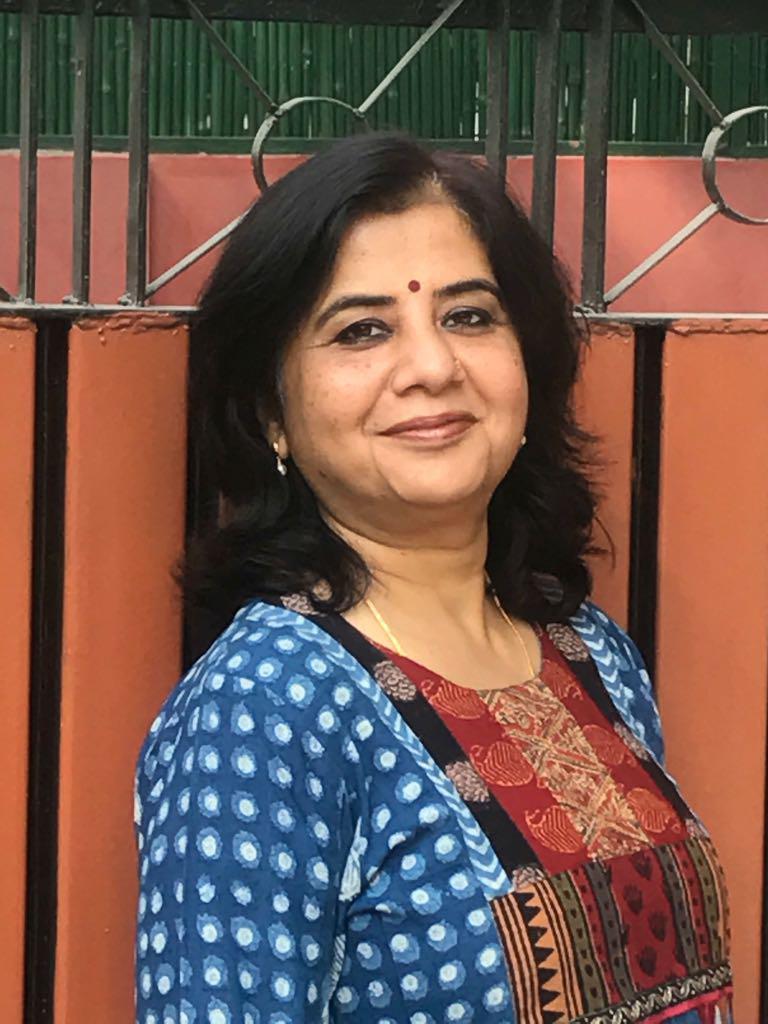
Sadhna Shanker
The month of October 2022, saw the highest monthly sale of Electric scooters in India. Moreover, the monthly registration for all electric vehicles crossed the one lakh figure. Compared to October 2021 figures, the increase was nearly 190%. For pollution drenched cities, switching to electric vehicles is an important milestone.
Electric vehicles are said to be the future, because they are eco-friendly and also have lower running costs. The first electric two-wheeler in the country was manufactured in 1996 by Scooters India Limited called the Vikram Safa. The first well know electric car in India was the Reva, which was unveiled in 2001.
Since then, globally electric vehicles have come a long way. Nearly all big manufactures of the world including Tesla, Mercedes Benz, Audi, Hyundai, Mahindra, Chevrolet, BMW, and Renault are making ground-breaking electric vehicles.
The Faster Adoption and Manufacturing of (Hybrid and) Electric Vehicles (FAME) – I and II initiatives of Government of India, begun in December 2015, are promoting manufacture of electric vehicles, charging stations and battery manufacturing. Nearly 16 states in the country have adopted their own Electric Vehicle policies. Presently, there are nearly 934 charging stations in the country with more being added both in the public and private sector.
Electric vehicles are good for the environment, as they do not rely on fossil fuels and have nearly zero tail pipe emissions. They are also silent, and their maintenance cost is low as the number of components in the engine are fewer as compared to combustible engines.
The most important and expensive component in the electric vehicle is its battery. They contain materials such as lithium, cobalt, manganese and nickel which are fairly costly. The factories that produce these batteries are called ‘Gigafactories’, because the battery output is measured in gigawatt hours. The term was first used by Elon Musk, sometime in 2013, to describe the massive battery production facility that the electric car company Tesla was building.
Traditionally manufacturing has been a linear process. Raw materials are transformed into finished goods, which reach the hands of the ultimate consumer. Once the life of the product is over, it is simply disposed of. Clothes, electronic goods, footwear, more recently masks and PPE kits are examples of goods that have been dumped indiscriminately after use. Such disposal often causes accumulation of non-biodegradable waste that pollutes the planet in different ways. According to a report of the World Economic Forum, less than 9% of the raw material used in manufacturing around the world is reused!
Gigafactories are moving towards the circular economy by aiming to produce their batteries from used batteries. This makes economic sense – the raw materials for batteries are expensive. By using the material from batteries that have reached their end of life, both the business and the environment benefit. There is no waste that remains to pollute the planet. In India, some of the bigger business houses are already in the process of setting up gigafactories for manufacture of batteries, and other critical components of the new clean energy eco-system.
Some big foreign car manufacturers are also setting up circular economy businesses, not just for batteries, but also for auto parts and cars. The effort is to recycle materials from used cars for fresh production.
The increasing use of electric vehicles, and adoption circular processes in the manufacturing of these vehicles is an encouraging sign. Other industries with huge wastages could also consider embracing recycling and reuse of their goods in manufacture. Greening the planet is not only a necessity, but also a collective responsibility.
Sadhna Shanker is a writer based in New Delhi, India.
Email: sadhna99@hotmail.com